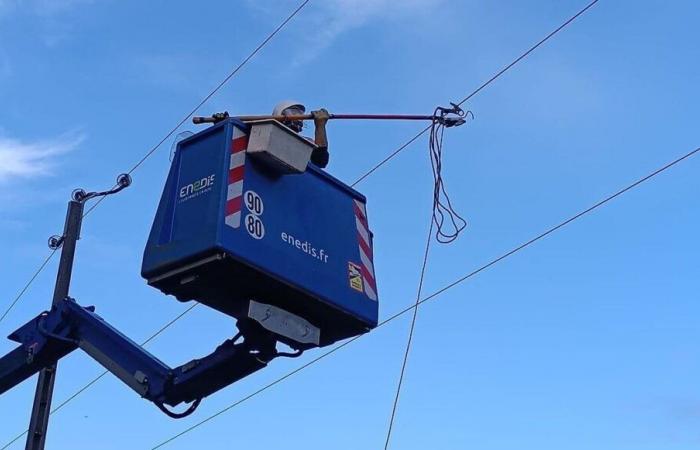
Gli ultimi quaranta abitanti del Puy-de-Dôme hanno riacquistato l'energia elettrica stasera alle 1:29 La rete è quindi completamente ripristinataon lavori di ricostruzione temporanei per garantire la sicurezza di tutti il più rapidamente possibile, spiega Pierre-François Mangeon, direttore di Enedis a Puy-de-Dôme. Verranno rafforzati nei prossimi giorni. IL forti venti Anche quelli in arrivo dal sud previsti per questa domenica 25 novembre vengono attentamente esaminati dall'azienda.
“I rami e gli alberi si trovano in alto sopra i supporti della rete. Anche con i cavi rinforzati, un albero che pesa diversi chili con la forza del vento provoca ovviamente danni“, spiega Nathalie Castex di Enedis Puy-de-Dôme. Per la prevenzione, Enedis ha squadre pre-mobilitate agire il più rapidamente possibile: 150 tecniciUN venti squadre di servizio e a dieci aziende di potatura. L'azienda mette in guardia anche sulla sicurezza: mai toccare un cavo quando è a terra. Invita chiunque a chiamare il call center risoluzione problemi allo 09 726 750 63.